Customized Shipping Container coatings are different from ship coatings. During construction, a certain proportion of diluent must be added and stirred evenly before use. Especially for epoxy zinc-rich shop primers, the added diluent is generally as high as 150%-200%.
Each Customized Shipping Containerr coating has a corresponding thinner and also stipulates the maximum dilution. In actual operation, it should be in accordance with the provisions of the Customized Shipping Container coating product manual. Using the wrong thinner or excessive dilution will reduce the construction performance and intrinsic quality of Customized Shipping Container coatings. For the operation of two-component container coatings, components A and B should be stirred separately, then mixed and diluted in proportion.
In recent years, in order to improve the construction performance and coating quality of Customized Shipping Container coatings, many coating factories have divided the diluents of the ring-neon zinc-rich primer into two types: winter use and ordinary type. When encountering a special painting environment, such as when the temperature in midsummer is above 30 ℃, or the exhaust air in the painting room is out of balance, the inner and outer paint films tend to become very rough.
For example, if the pigments of the Customized Shipping Container paint are seriously precipitated rather than hardened, if they cannot be stirred up, the upper layer of paint cannot be used only, and the bottom plate should be discarded. In this way, the performance of the paint will change, and the quality cannot be guaranteed. For such Customized Shipping Container coatings, if it occurs within the validity period of storage, it should be returned to the coating factory for replacement. Precipitated, hardened and gelled container coatings cannot be forcibly diluted and used, and should be discarded.
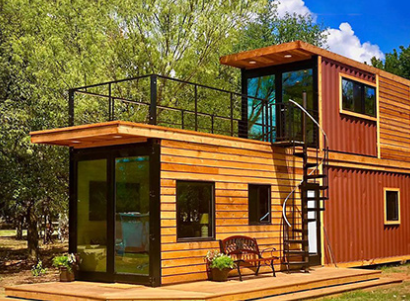
The epoxy zinc-rich primer, epoxy primer, and epoxy interior paint for thousands of Customized Shipping Container are all chemical coatings. They are two-component coatings, that is, the base material and the curing agent are packaged separately and mixed when they are used. Before mixing, the base material (A) and the curing agent {B) should be stirred separately in advance, and then mixed while stirring until the whole is uniform. After the A and B component paints are mixed, they will undergo a chemical curing reaction. In order to ensure its construction performance and curing performance, a pre-reaction period of 20-30 minutes is required before the paint is used, which is also called the aging period. It should be according to the container coating product manual. Requirements order to guarantee the specified curing time.
It is also due to the film-forming mechanism of the chemical reaction of the two-component coating that the components A and B must be used within a specified time after mixing. If the amount exceeds this specified time, the coating will lose fluidity and even cure. This period is called the application period (or use period) of the two-component coating. Generally, the pot life of two-component coatings is about 8 hours at a temperature of 20°C; when the temperature exceeds 30°C, the pot life of two-component coatings can only be controlled at about 4 to 5 hours. Coatings beyond the pot life must be discarded, otherwise the quality of the coating film will be seriously affected. Therefore, in production, it should be mixed in proportion according to the quantity of boxes and the amount of paint required, so as not to cause waste.
Comment
(0)